Safety on the Construction Site: A Guide to Using Twiceme Technology
Implementing new PPE in an organization can be a time consuming process, involving several factors to take into account. In this guide, we’re going to break down the important considerations when it comes to Twiceme and its usage on construction sites.
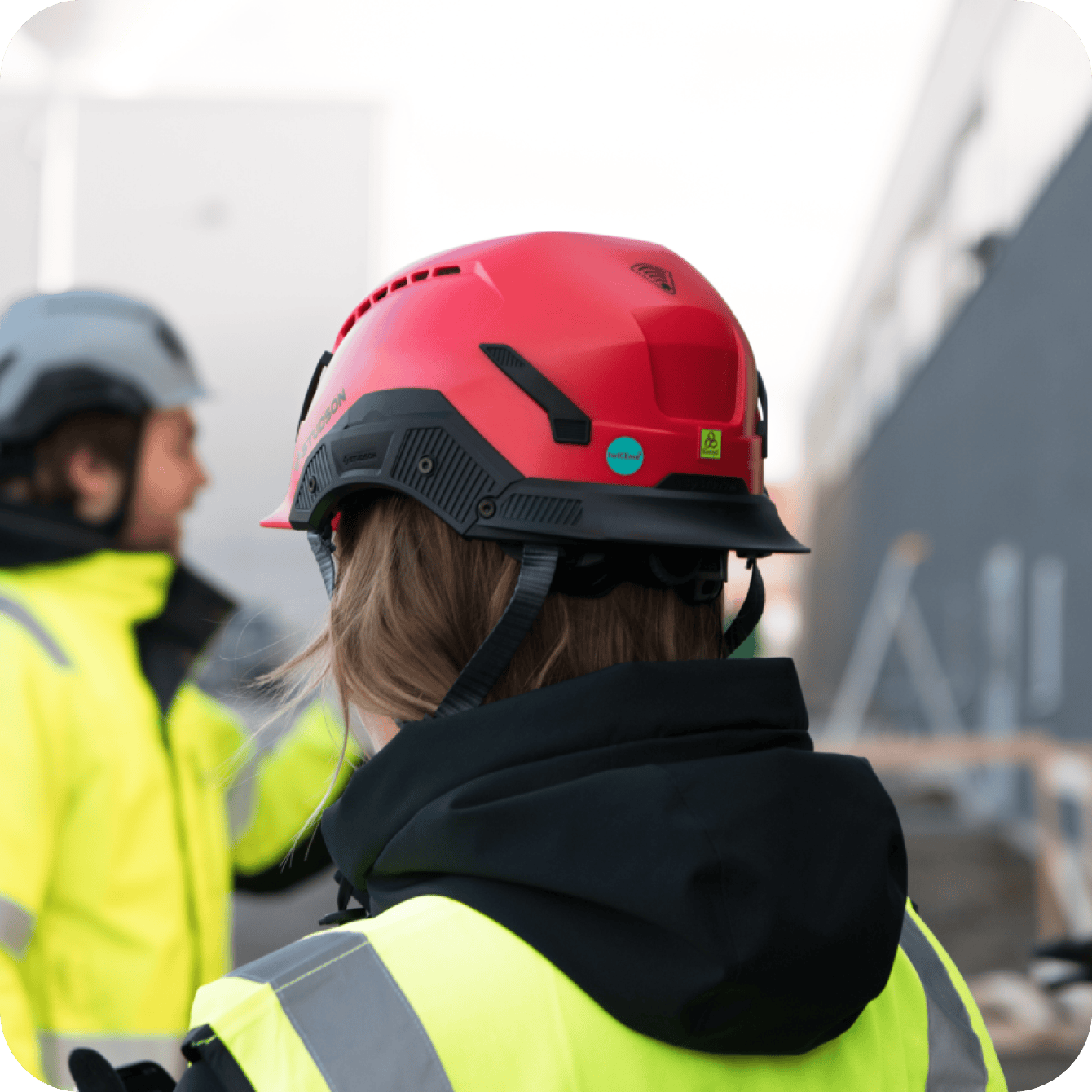
Introduction to Twiceme
Implementing new PPE in an organization can be a time consuming process, involving several factors to take into account.
In this guide, we’re going to break down the important considerations when it comes to Twiceme and how using equipment containing the technology can aid in enhancing safety at the construction site. And result in thousands of dollars saved over its lifetime.
- We start with some important considerations to take when deciding on equipment for the site.
- Then we move on to discuss how to test out Twiceme’s functionalities and implement it at the worksite.
- Furthermore, we’ll briefly touch on the cost savings we’ve seen with some large contractors, who might no longer need to spend thousands of dollars (literally) on ICE stickers, expensive software for inspection systems, and more.
But before that, maybe you’re unfamiliar with Twiceme. So, what is it?
To answer that question, let’s think about something.
Some may not agree, but after working with over 250+ rescue organizations worldwide, we know one of the problems rescuers face is to arrive at an accident site without knowing anything about the person.
Twiceme was born from this realization. To build a tool that allows bystanders to become helpers through providing the right information about a person who’s contacting emergency services.
Through Twiceme’s core product, the gear-based medical ID, bystanders can tap the integrated hardware to access safety information about the person. Such as medical information, diseases, insurance information, ICE contacts and more.
This results in the rescuers arriving more prepared at the accident site.
But there’s more. Hopefully, accidents happen rarely. So, how can we make sure that people are safe the rest of the time? Now we’re in the non-emergency, or precautionary stage.
Why safety measures should be prioritized
For construction sites, it’s of crucial importance to use equipment that is in good shape and controlled regularly to comply with regulations and local authorities. So, right inside of Twiceme, there’s a plethora of features for safety officers and contractors to keep track of the usage and durability of the equipment. Because if the workers use a safety harness that’s not in top shape, the risk of injury most likely increases.
And, as you probably know, the construction industry is plagued by high injury statistics.
Here are some findings about the cost of injuries at construction worksites, its implications, and potential solutions that might open your mind as to why things must change. First and foremost to save lives, but also to decrease costs:
1. Construction injuries cost $11.5 billion in the US, with $4 billion in fatalities and $7 billion in nonfatal injuries.
2. The total cost of work injuries in 2021 was $167.0 billion in the US, including wage and productivity losses of $47.4 billion, medical expenses of $36.6 billion, and administrative expenses of $57.5 billion.
3. Injuries and ill-health in the UK construction industry cost upwards of £16.2bn per year.
4. The 10 most common injuries in the US construction industry cost companies more than $11 billion annually.
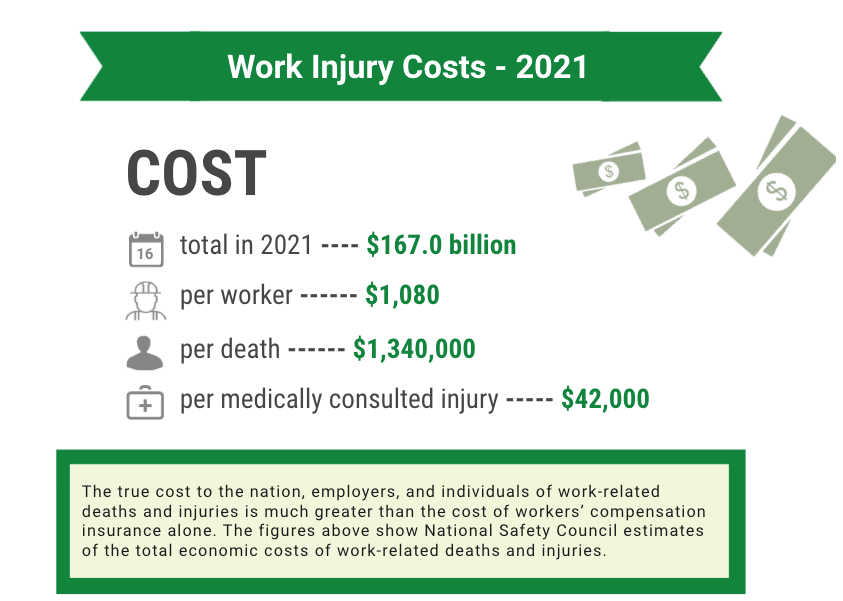
The cost of an accident in the workplace has been defined as “effects on the costs […] of a company that would not have been borne if the injury/accident had not taken place”. This means that, if measures can be put in place that reduce these injuries, and the implications of an injury, the construction industry can save billions of dollars each year.
Now, let’s dive into what makes equipment good and how Twiceme can help spread a safety-first mindset at the site.
Section 1: Choosing the Right Equipment.
When deciding on the right equipment for the construction site, numerous factors must be considered. Unfortunately, it’s often price that is the top priority for many contractors. This, however, has begun to change.
Workers are no longer accepting substandard PPE. In that case, why even use a helmet at all?
What’s important to note is that safety should be the number one priority in an organization. Not to barely comply with regulations.
Even though OSHA regulations state that head protection should be used at the site, most larger contractors are now adding the requirement to use chin straps as well. Which is a step in the right direction.
For decades, the sports industry has been innovating and taking the lead when it comes to safety. Construction workers, however, have had to make due with subpar helmets and harnesses.
Here’s where companies like Guardian in the harness industry, and Studson in the helmet space, are becoming the industry leaders by bringing innovative technologies and premium products. And, it seems like it has paid off.
It’s usually the case that the goliaths of an industry are slow movers, they’re the incumbents, and new innovators move up and shape the direction of the industry. It’s one of the reasons why few S&P 500 companies make it past 100 years. They grow slow and lose innovation.
But not Guardian, one of the world’s largest producers of safety harnesses. They saw the trends of a safety-first mindset amongst workers and contractors, and decided to move towards more premium-style harnesses, such as the B7 harness.

What’s more, regulations are starting to move forward. Especially in Europe and the Scandinavian countries. The US is usually slower moving when it comes to enforcing regulations, but the EU is taking worksite safety seriously. Not only when it comes to better equipment choices, but also in terms of enforcing identification of workers at the site, and more.
What’s interesting about Twiceme, for example, is that it can be used as an all-in-one tool to solve many of the regulation issues that contractors face in the coming decade, unless they want to change equipment more often than needed.
In summary, when choosing the equipment for your worksite. Make sure to take a long-term and holistic view of the PPE.
- Can this PPE add elements that would allow us to remove costs in other places?
- What’s the regulatory landscape going to look like in 5 years? What tendencies are we seeing?
- Will higher quality equipment result in increased work-efficiency? Can it decrease the costs of liability because the number of injuries also decreases?
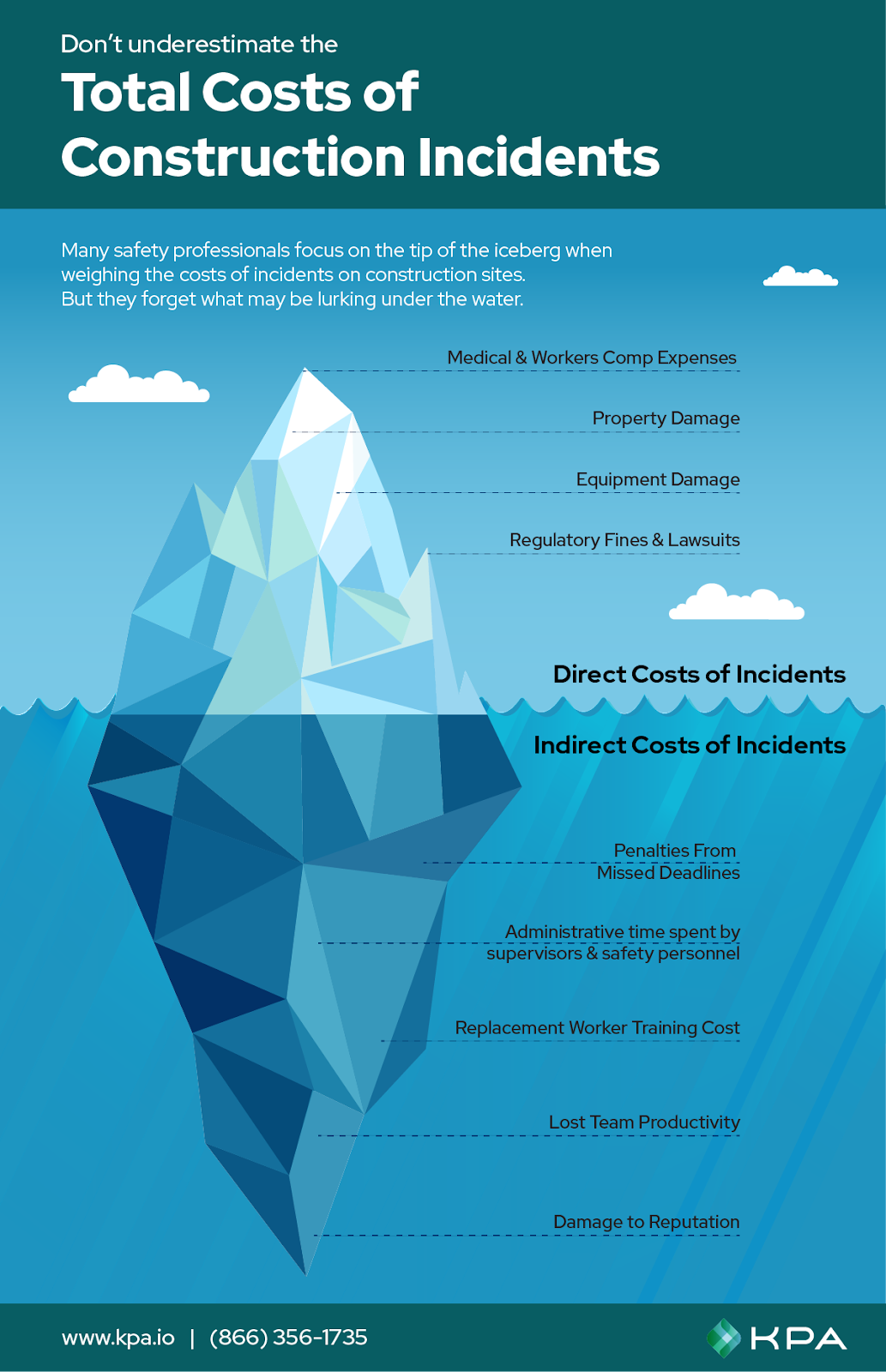
The issue here is that for large contractors, they receive a budget each year to spend on PPE. Then, the IT department receives a budget to spend on software (e.g. inspection systems). And so forth. Here’s where these departments need to work together to see if two problems can be solved with one solution. Such as equipment that already contains digital aspects.
You can find all construction equipment that contains Twiceme here, such as safety harnesses and helmets.
Section 2: Receiving and Testing Twiceme
Ordering Twiceme - Working With Selected Brands
If you’ve decided that adding safety technology to your PPE and workforce, and Twiceme is a viable option for you, then it’s time to scout the market for the right manufacturer.
We do not sell our hardware as an add-on or separately, because we believe it should be standardized across the world. Otherwise, the usability quickly decreases as rescuers and helpers will find it difficult to know where to look for the symbol.
Look through the products found with Twiceme by checking out our equipment page, or if you’d like your current supplier to have Twiceme in the range you normally buy, feel free to reach out to us. You may also reach out to us for any guidance on which product might best suit your needs from our current partners.
Testing out the functionality of Twiceme
Now, what if you’re at the point of having ordered PPE equipped with Twiceme.
How do you get started using it?
How to implement it at the worksite to ensure the safety of your employees?
First of all, Twiceme is simple to use and to get started right away. Follow the instructions in the image below to get started.
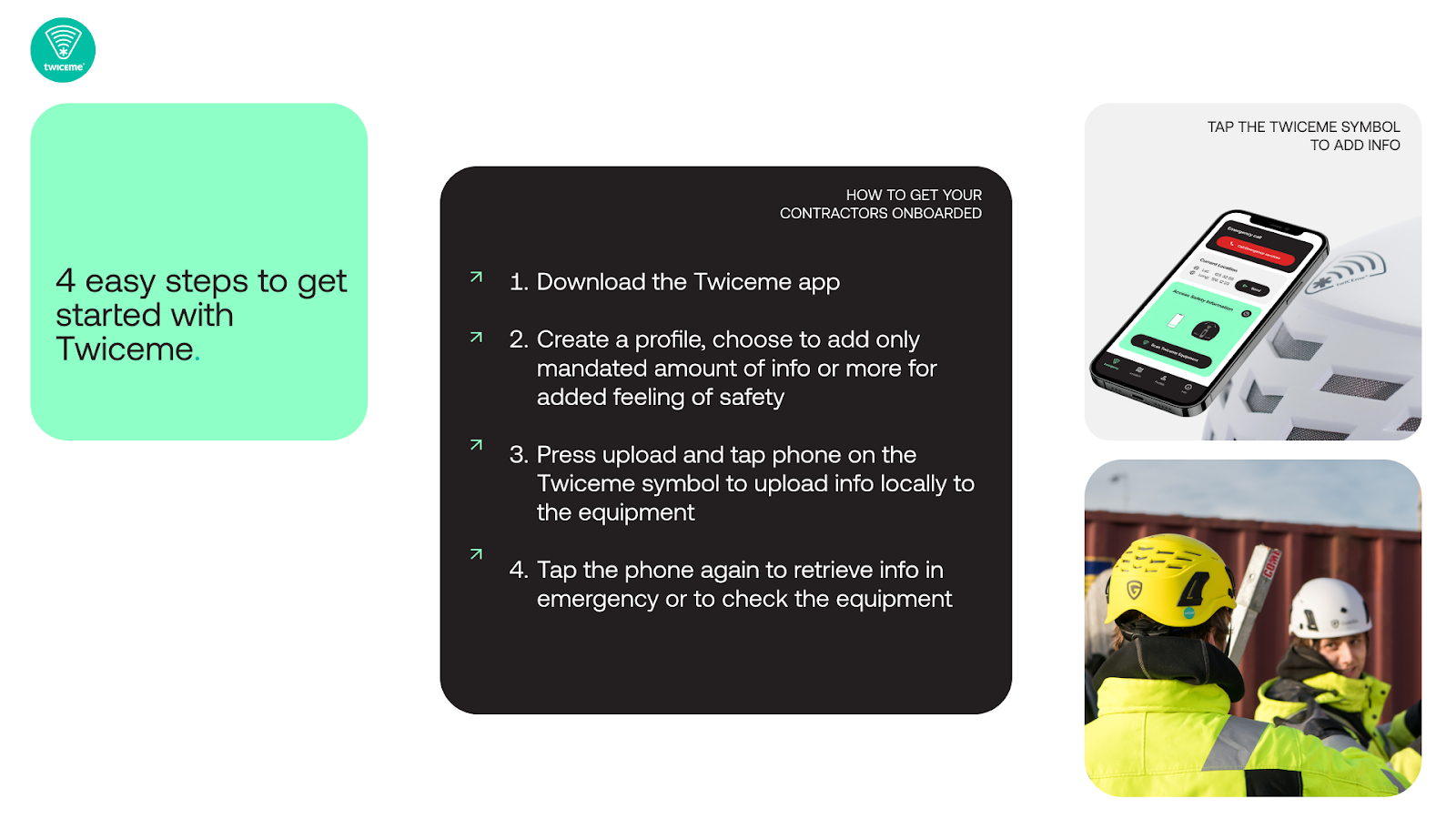
Now you’ve uploaded the information to the equipment. Locally stored. Why would you do this, though?
As mentioned before, in case of an emergency, it’s paramount that you know who to contact, and who the incapacitated person is. The more information rescuers have on their hands when arriving at the accident site, the better they can make an hypothesis of the best care to give.
Also, when you uploaded the information, you did so to a chosen equipment in the library. If this was simply a trial run for testing out the functionality, maybe you simply chose an “unlisted product”, but otherwise you’ve chosen your equipment. And that means the information about your equipment is now stored locally in the equipment.
This allows you to follow up on the lifetime of your equipment, as recommended by the manufacturer. Let’s say your helmet has a 10-year recommended lifetime, then in one year (and every year after that) you’ll be asked a series of questions to evaluate if maybe you should look into changing the equipment.
Questions such as:
- Are there any noticeable cracks or marks on the shell?
- Has the helmet experienced any falls or drops in the year?
- Is the color faded by the sun? Has it been put through extreme heat? Etc.
The questions vary depending on the equipment of choice. A firefighter helmet needs to be checked differently than a harness.
Also, if you use equipment that has the inspection functionality (currently exclusive in safety harnesses from Guardian), then you can also integrate the inspection flow with safety officers right in the app, sign them off when done and export to excel or pdf. Right inside the app. More on this below.
Section 3: Implementation on the Worksite
It’s usually difficult to bring company-wide change. Everyone knows and understands that. However, after having invested in equipment that can decrease overall injuries, shouldn’t it be a priority? Twiceme does just that, which is why it’s important to get wide-spread awareness and implementation in the workforce.
The first thing that should happen after (or during) equipment is being given out to employees is to have a stand-up. Which most teams have in the beginning of the workday or workweek. In that meeting, take 5-10 minutes to describe Twiceme and what it can do for employees. Not sure how to do that, or would you like a presentation to show/send as emails to workers? Reach out to us and we’ll be more than happy to help.
During the stand-up, make sure everyone downloads the app and explores its functionalities. It takes about 1 minute to create a safety profile, so make sure everyone does it. On the worksite, there are usually a few mandatory pieces of information the contractor needs (and wants) everyone to store on their equipment.
This can be:
- The closest foreman’s phone number and name.
- The equipment’s first date of usage.
- What contractor the person belongs to.
- At least one ICE contact number, etc.
The rest is up to the worker to decide how much or little they want to share. Make sure to share how valuable this information is to rescuers, and the more information they share, the more informed decisions and hypotheses they can make in case of an emergency. Also, be sure to highlight that the safety information they add in their profile is never stored in any database. It’s locally stored and ensures the personal information is not shared unless someone scans their information.
The uploaded information can also easily be removed from the equipment, for example when the worker leaves for the day and the equipment might be used or accessed by someone else the next day. Just make sure that people remember to reupload their information every morning in that case.
Finally, make sure people upload their information to their equipment. This ensures everyone has their information uploaded, plus it gives everyone a chance to understand how to do it (upload information). It can be a little tricky the first time. As a final verification, you can also ask everyone to scan their own or someone else’s Twiceme to ensure the information is uploaded correctly, and that they know how to access the information in case of an emergency.
The benefits of the non-emergency features
The beautiful part of having everyone go through the process of uploading their equipment is it ensures that you can use the other features in Twiceme. Such as equipment health and the inspection system. You can obviously not use it unless a personal and equipment profile is uploaded to the equipment.
These added functionalities ensure people can be proactive about safety. Safety officers can speed up their workflow, and won’t need to spend excess amounts of time going through everyone’s equipment. It also ensures that people are actually using Twiceme and its safety functionalities.
If we discuss the equipment health functionality for a second, it’s a great way for workers to always be mindful of how long they’ve used their equipment. It also opens up their mind regarding safety and helps them in the right direction by asking questions they have to answer.
Section 4: Ongoing Usage and Benefits
When Twiceme is successfully implemented widespread on a worksite, it can have a positive impact on safety mindset and help aid in emergencies. One of our partner’s customers incorporated Twiceme to all their 7000 employees and even pushed their subcontractors to use it. This brings added benefits beyond safety, since it allows them to save thousands of dollars each year on ICE stickers and more. Something that many contractors see as a “necessary evil” to combat high injury statistics at their worksite.
But it doesn’t have to be like that. Because the problem with these stickers, and other solutions like them, is that they fall off and are not standardized. Which means each worksite and subcontractor might use different solutions. This makes it difficult to have an SOP which everyone at the worksite knows how to follow.
Conclusion:
In summary, Twiceme is a safety technology that can enhance safety at worksites, if implemented properly. It obviously requires a short introduction period before it can be implemented and used properly. As with all technologies, it required buy-in from management and the people on the worksite. But comparing it to many other solutions, it can be both a cost-effective and easy solution to an otherwise big problem many contractors face.
If you’re interested in implementing Twiceme at your workplace, but aren’t sure where to start, feel free to reach out to us for more information.
Discover More Exciting Content.
Explore more related articles
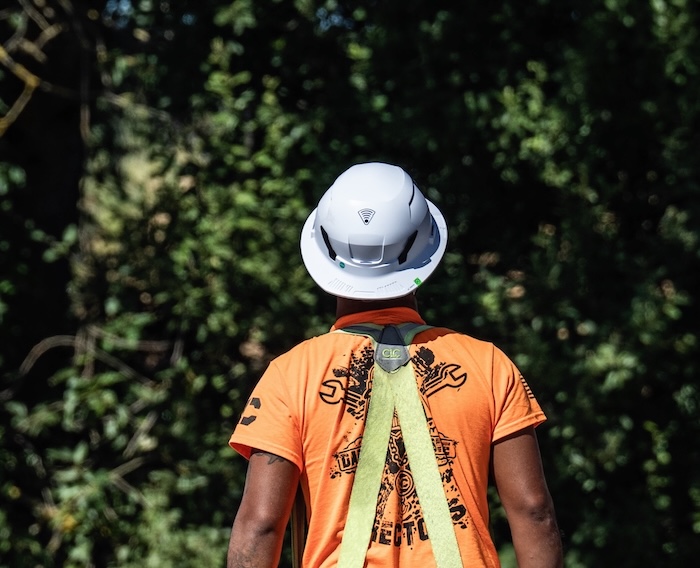
The Digital Divide in Construction Safety
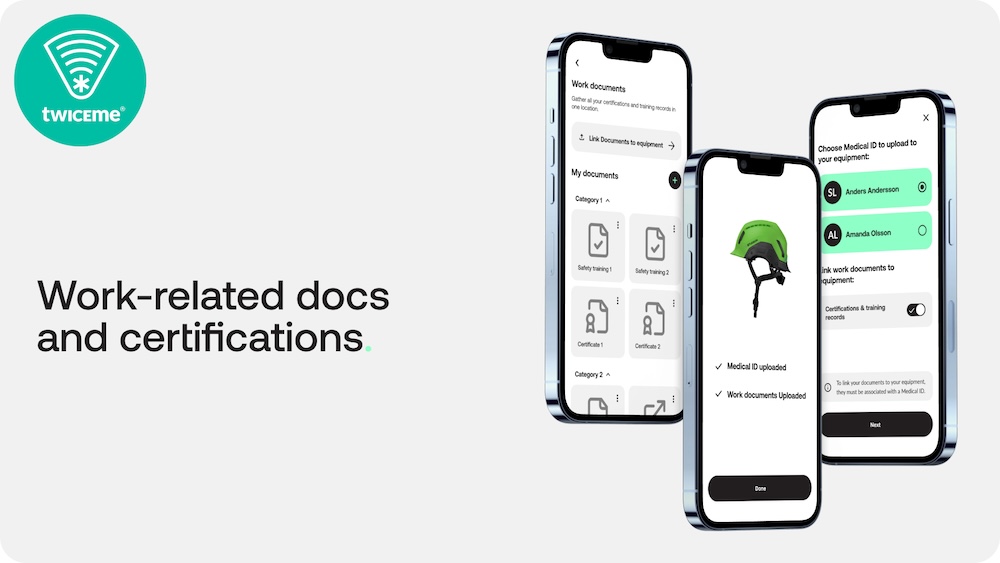
Introducing Twiceme's New Feature: Work-related Documents and Certifications Upload
.jpg)
Twiceme University: Newly Launched Online Education Platform
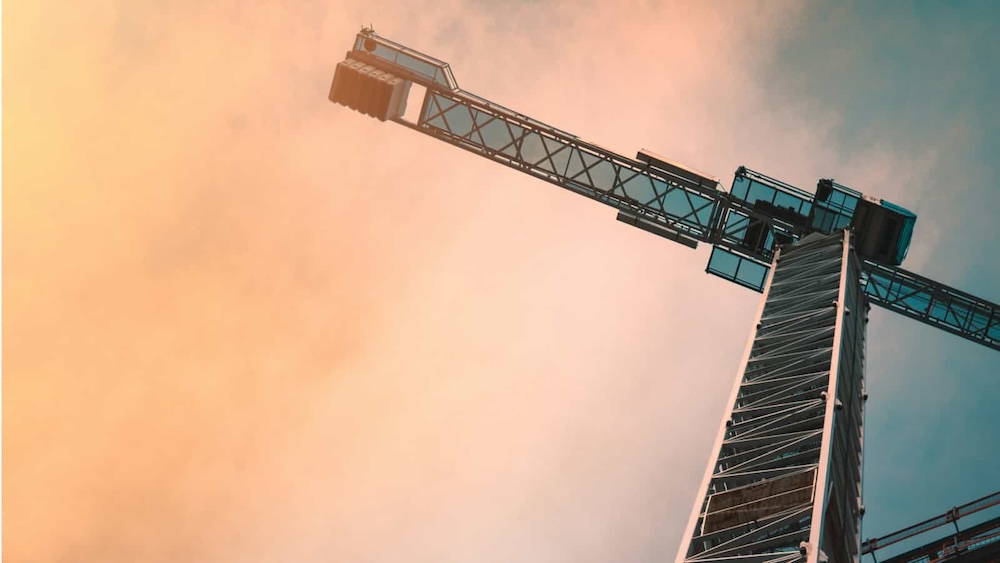
A Conversation with Daniel Ruane, VP of Safety at Pepper Construction
.jpg)
Introducing the Diamondback 701 Vest with Twiceme Help the Helper Technology
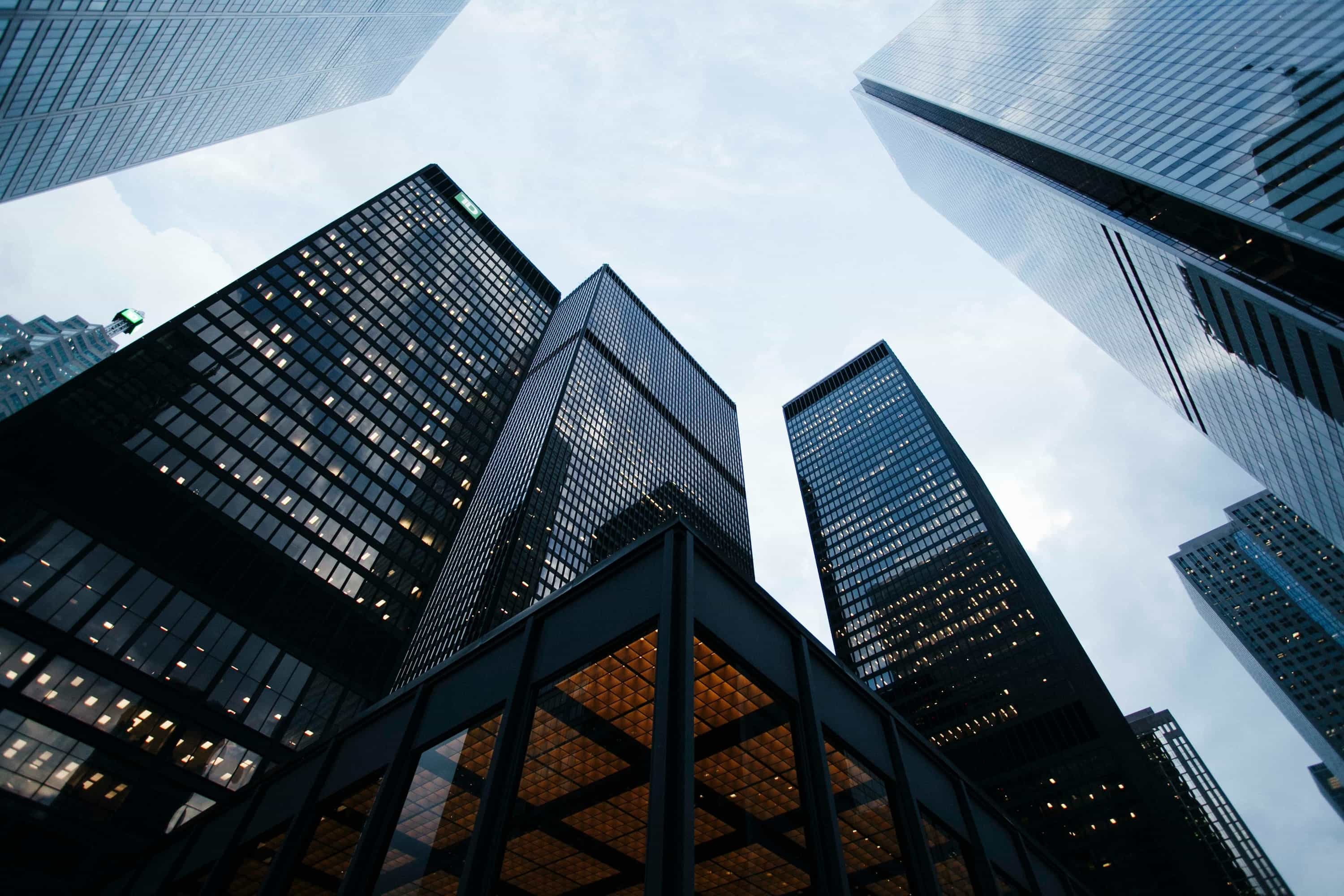