A Conversation with Daniel Ruane, VP of Safety at Pepper Construction
Daniel Ruane, the Vice President of Safety at Pepper Construction, brings over two decades of experience and insights to the field. This article delves into his professional journey, the changing landscape of construction safety, and the future innovations that show promise to enhance worker safety.
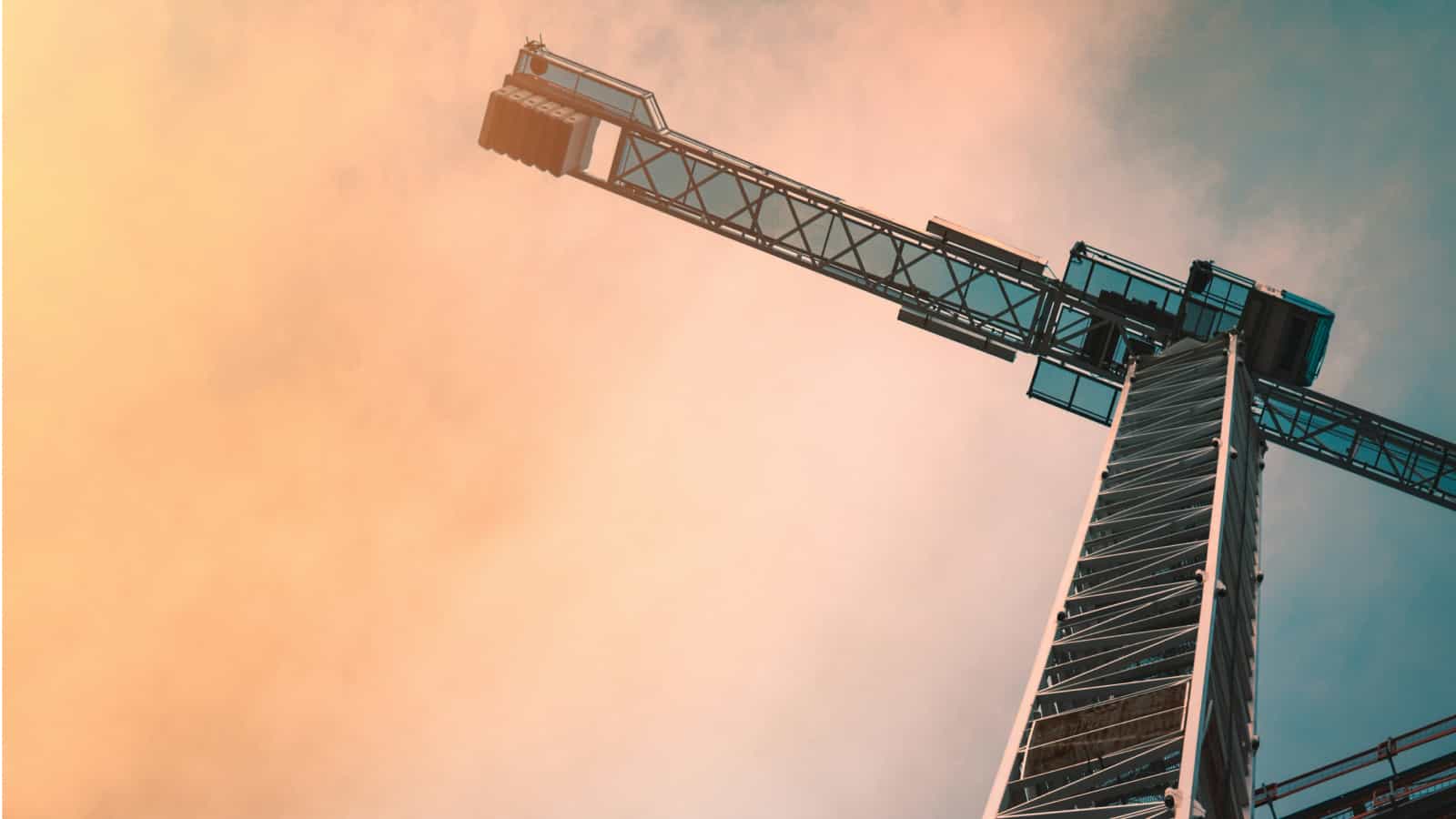
In the ever-evolving construction industry, safety remains a paramount concern. Daniel Ruane, the Vice President of Safety at Pepper Construction, brings over two decades of experience and insights to the field. This article delves into his professional journey, the changing landscape of construction safety, and the future innovations that show promise to enhance worker safety.
Daniel's Background and Career Path
Daniel Ruane's journey into construction safety began at Illinois State University, where he initially pursued accounting. However, deciding at 17 what you want to do for the rest of your life can obviously be a daunting task. But a desire to avoid a sedentary office job quickly became clear, and a family background in construction trades led him to switch to occupational safety and health.
Over the years, he’s worked with four major general contractors in the Chicagoland area, gaining valuable experience and perspective by engaging directly with the workforce. Since all of them are self-performing contractors, meaning they employ all types of roles, from carpenters to concreters, it has provided Daniel with a unique insight into the practical implementation of safety measures. He explains, "This hands-on experience is invaluable. It allows you to see the immediate impact of safety protocols and understand the daily challenges faced by workers."
Daniel emphasizes that even though subcontractors are sometimes used, self-performing contractors have much more control over which safety measures to implement and how they’re followed, thus accumulating extensive real-life safety experience. "Having a direct line of communication and control over safety procedures ensures a safer environment for everyone involved," he adds.
Building a Safe Working Environment
When we talk about safety, numerous things have changed over the years since Daniel began working in the industry. But, one of the most important ones, in his opinion, is the change from safety managers being seen as nothing more than “safety cops” to becoming safety partners by helping more workers go home uninjured while allowing them to continue to work efficiently.
Previously, the safety managers used to be asked by their supervisors “how many tickets have you written today?”, which never really sat well with him. Because that meant that the workers and safety managers weren’t really on the same page nor team. The only goal really for the safety manager was to react to incidents where workers didn’t follow protocols and regulations, instead of working together with the people on the sites to eliminate the reasons and causes as to why incidents happened in the first place!
Daniel remembers one time early in his career when he was out at a job site where a relatively unsafe contractor was working, and his supervisor came by to ask him “how many tickets for not wearing safety glasses have you written today?” because that was a low hanging fruit. And the only thing Daniel would think about is; “we have so many bigger problems to tackle before we start even thinking about safety glasses on this site. People are literally not utilizing fall protection when working on top of the buildings.”
Over the years, injury statistics have gone down quite a lot. Something that can likely be attributed to better equipment and laws, but ultimately it’s that companies learn from previous incidents. And that’s where a culture of trust is so important, he mentions. Because if the workers don’t trust the safety managers, they won’t report on “non-fatal incidents” or incidents that aren’t required to be reported because nobody got injured. Because of a fear of being fired or similar. However, if there’s trust, they might do it. Which means that the company can learn from these smaller incidents and near misses, and thus avoid a large disaster further down the line.
The Trends and Case for Smart Equipment to Lower Fatality Rates
Over the last two decades, injury rates have decreased. However, the fatality rate in the construction industry has remained relatively stable (and high compared to many other industries), which to many people is a bit of a mystery.
But why are the non-fatal injuries going down? One of the main demographic trends, in Daniel’s opinion, is that younger workers are entering the industry. And these younger individuals are brought up with a safety-first attitude and mindset. Having used bicycle helmets all their life and being educated on the dangers of not wearing PPE, much like what our interview with Chris Sackett, ex VP of Bell, revealed, it’s clear that they are changing the industry for the better.
Another large reason is training. In the US, trades are largely developed around a strong union presence, where you’re not allowed to work as an electrician unless you have the correct education and have completed an apprenticeship program. These specific trades also come out of union halls, so whenever a contractor needs a plumber or electrician, they call these union halls to get a few to their sites. And these unions do a lot of training. Not only that, ongoing training is much more prevalent in today’s society than 20-30 years ago. Both because of harder laws, but also because technology and apps open up opportunities for easy ongoing (and personalized) training.
With the usage of AI, contractors can train their employees specifically in the way that it most benefits each person. And many platforms are starting to integrate these types of functionalities.
"The thing that will be the hardest to engineer away, at least for now, is the human factor. We’re still human beings performing very complex and often heavy tasks, which put a lot of pressure and physical strain on the body," Daniel notes. "Which is where the next innovation comes in, exoskeleton equipment that aids the human body in performing these tasks."
Innovative Safety Solutions: Exoskeletons and AI
One of the most exciting developments in construction safety, according to Dan, is the advent of exoskeleton technology. "Exoskeletons have the potential to revolutionize the way we work by reducing physical strain and minimizing the risk of injury," he says. These wearable devices can assist with heavy lifting and repetitive tasks, making the job safer and more efficient for workers.
Another area of interest is VR and AI safety training. "By using virtual reality and AI, we can simulate hazardous situations and train workers on how to respond safely," Daniel explains. This immersive training experience can help workers better understand the risks and learn how to mitigate them effectively.
In addition to advanced training methods, digital tools for quality control and audits are making a significant impact. "Data is invaluable in understanding commonalities and correlations among injuries and fatalities," Daniel emphasizes. "Digitizing inspections and audits allows us to gather precise data and identify trends that can help prevent future incidents."
Pepper Construction has also developed in-house tools like a fall-protection harness inspection app. "Most apps on the market come from manufacturers and only allow you to use their own equipment. But we use many different manufacturers, so we needed a more versatile solution," Daniel explains.
When implementing new PPE, tools, or processes, the most important part is to ensure the people on the ground, who are actually going to implement and follow them, have ownership. "It’s crucial to involve workers in the decision-making process and show that their opinions are valued," Daniel says. "This not only improves compliance but also fosters a culture of safety and trust."
Smaller but equally important innovations include digitizing processes that were previously done manually. "I love data," Daniel admits. "Using apps for quality control and audits allows us to gather precise information and identify trends and correlations among injuries and fatalities."
Creating Internal Alignment Around Safety
There are a few key things, in Daniel’s opinion, that bring the company together around safety.
The first one being to ask for input and inviting the workers on the sites to the table for discussions around subjects that will impact them. They’re the ones who will use the equipment and will ensure a safe environment on the sites. Also, they’re the experts in using the equipment and know what is useful, comfortable, and more.
Secondly, that the leaders of the organization, whatever level they’re on, speak and act authentically around safety.
“It’s very rare that the person under you will behave in a compliant and safe manner, if you yourself don’t care. Or maybe even work against some regulations set by the organization”, he mentions.
We’ve all probably seen this, where the senior person says “don’t worry, I know management has said this is how we do things, but here’s how we really do it”. This quickly turns into a problem where people stop listening to compliance issues, thus leading to injuries happening.
At Pepper, even President Scot, participates in safety audits and involves everyone around the safety culture. On that note, the President at Pepper even goes out to the field to ask the workers how the company can act in a better way and support them in a better fashion. Which really speaks of a strong message of support to the workers.
“You’re the most influenced by your direct supervisor. So really spend much more time with the supervisors”.
So, even though there’s a lot of cool tech out there and ways to engineer some dangers away, nothing comes close to having a safety-first mindset and a great company culture. Of course, tech can aid a strong organization.
The Power of Data in Safety Management
Another critical aspect of modern construction safety is the use of data. "Data allows us to see patterns and trends that we might miss otherwise," he says. "For example, we've developed an app for inspecting fall-protection harnesses that collects data on how often they're used and when they need maintenance."
By analyzing this data, Pepper Construction can identify potential safety issues before they become serious problems. "We've also worked with our insurance company to identify over 40 precursors that are often present in serious or fatal incidents," Daniel explains. "This helps us focus on preventing these situations rather than just reacting to them."
Conclusion: A Vision for the Future
Daniel’s passion for safety is evident in every aspect of his work at Pepper Construction. From his early days as a safety manager to his current role as Vice President of Safety, he has always prioritized the well-being of workers. His forward-thinking approach to integrating technology, fostering a culture of trust, and leveraging data to drive safety improvements sets a high standard for the industry.
"We have to continue evolving and finding new ways to keep our workers safe," he concludes. "Whether it's through better training, innovative technology, or creating a culture where safety is everyone's responsibility, we owe it to our workers to make safety our top priority."
Daniel’s insights and initiatives demonstrate a clear path forward for the construction industry, one where safety is not just a regulatory requirement but a core value embraced by every worker and leader alike.
Discover More Exciting Content.
Explore more related articles
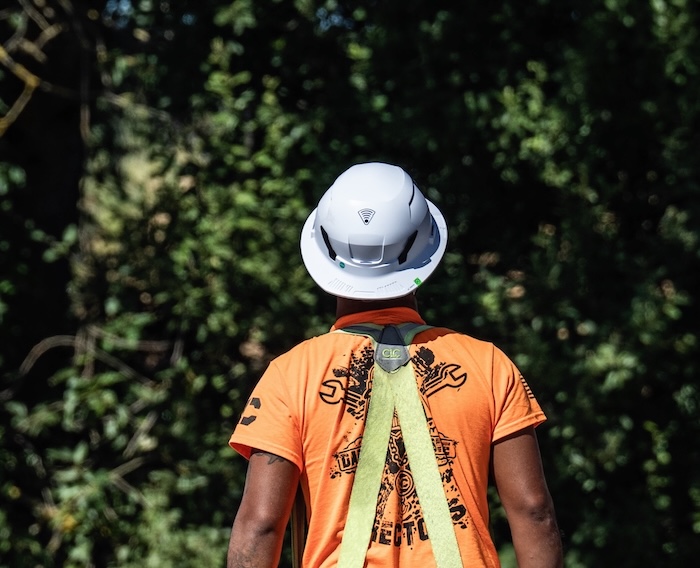
The Digital Divide in Construction Safety
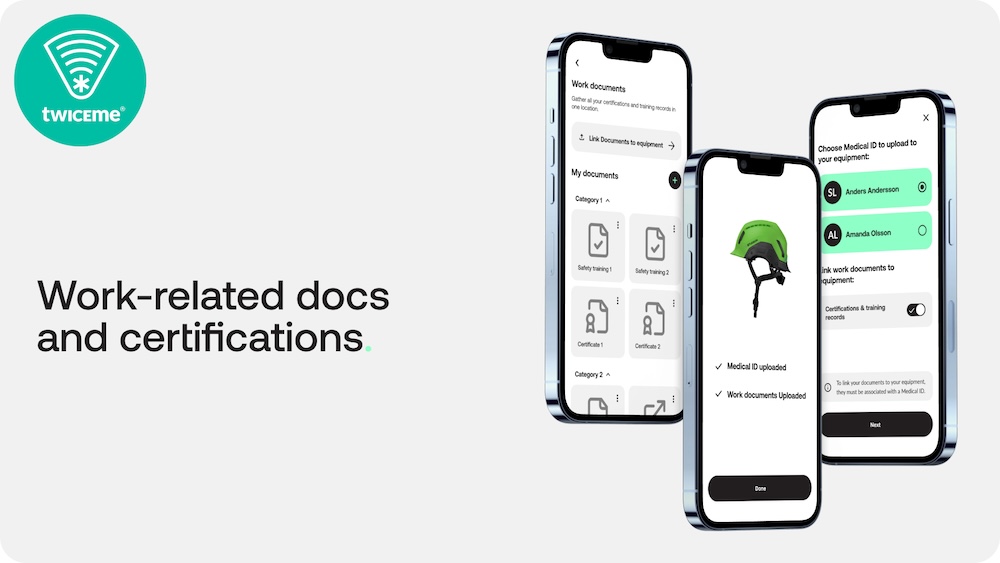
Introducing Twiceme's New Feature: Work-related Documents and Certifications Upload
.jpg)
Twiceme University: Newly Launched Online Education Platform
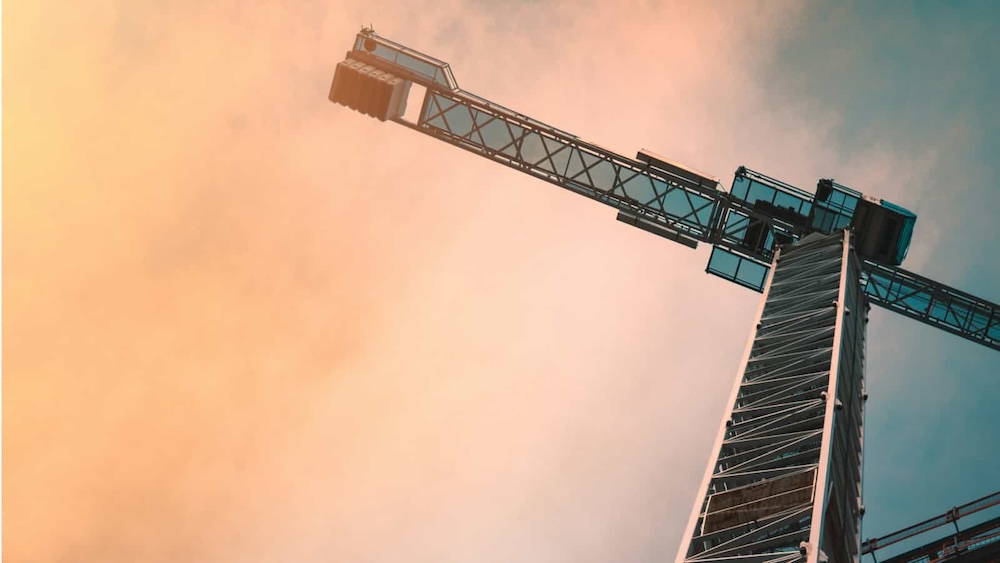
A Conversation with Daniel Ruane, VP of Safety at Pepper Construction
.jpg)
Introducing the Diamondback 701 Vest with Twiceme Help the Helper Technology
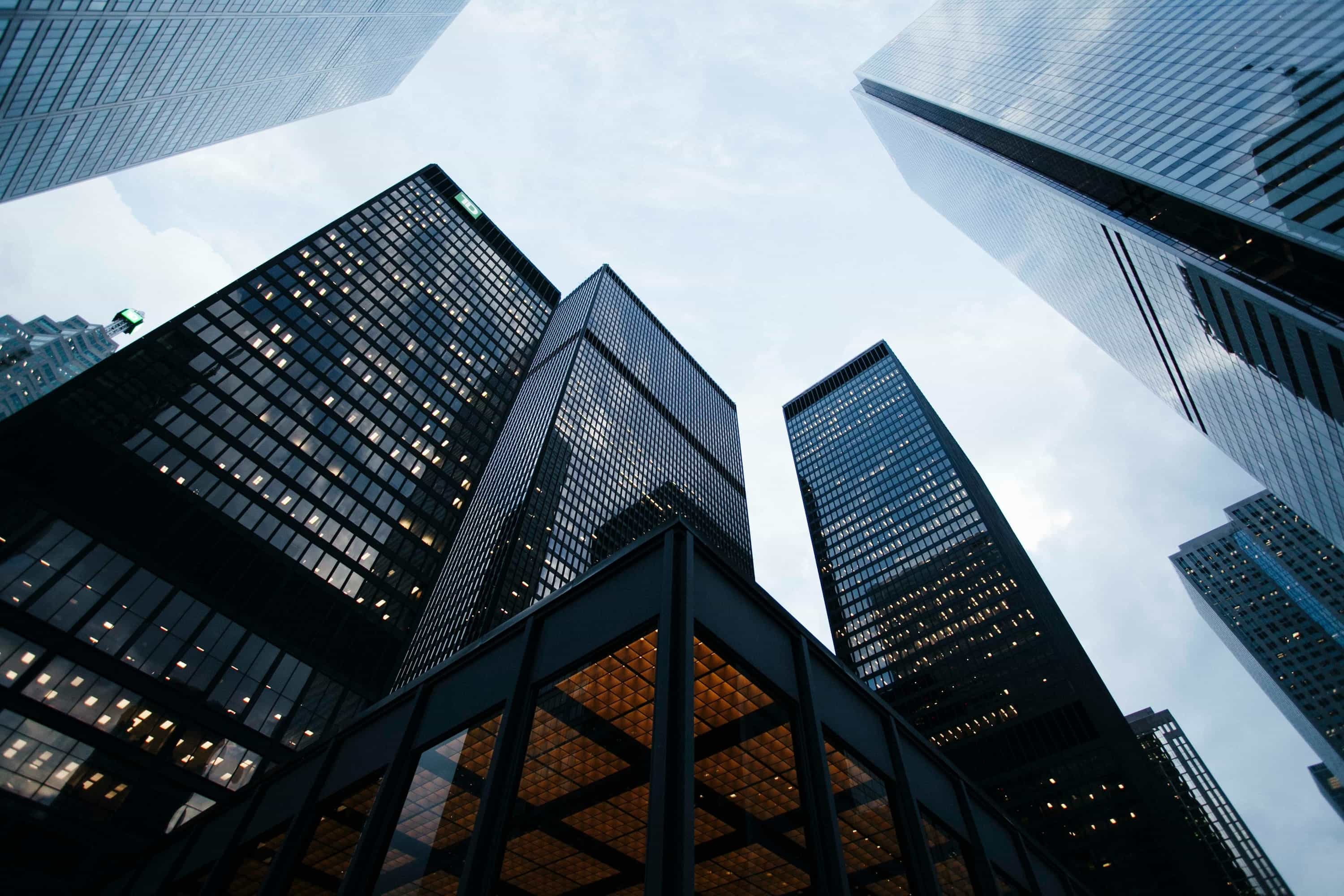